CERTIFICATIONS
All models shown in this catalogue comply with the international ECE 22.05 or ECE 22.06 standard, DOT FMVSS NO. 218, China Compulsory Certificate, etc.
The first important characteristic of Aegis is its credibility as a producer; a credibility which is not only the result of its professional, but also, and above all, of its continuous commitment to safety and quality.
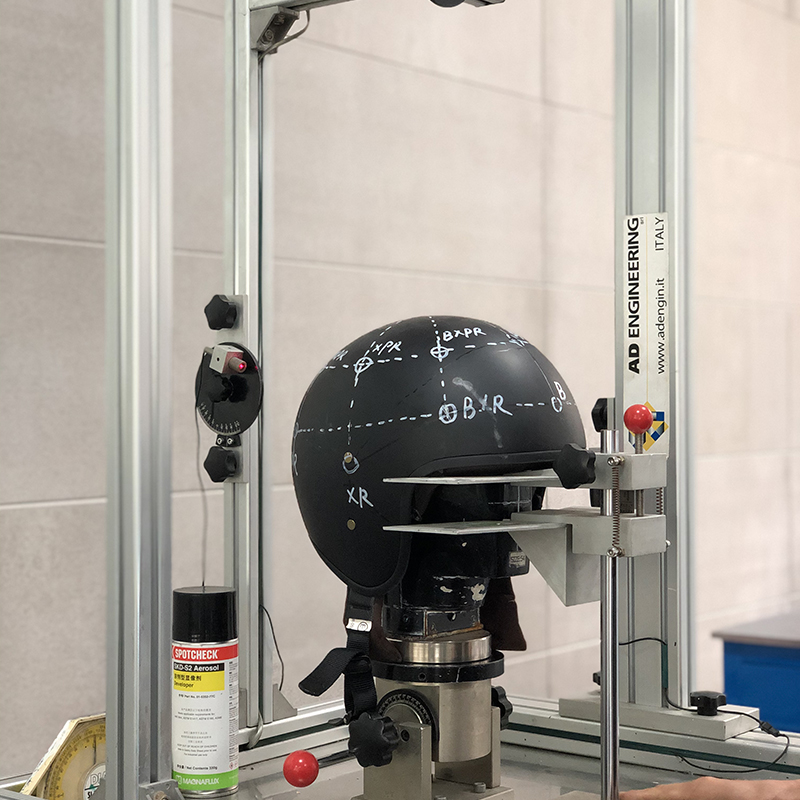
INTERNAL LABORATORIES
Aegis sets up own internal laboratory which play an essential role both in the development stage of the product and in daily production.In order to meet the ECE / DOT/ CCC etc, impact,penetration, tests on retention systems and helmet loss tests are carried out on helmets, while the visors are subject to optical and resistance tests. Specific equipment and machinery furthermore allows for the carrying out of tests required by other international regulations.The helmets and visors are then passed to external independent laboratories run by third parties, in order to obtain the relative homologation and certification, therefore allowing mass production to begin. The laboratory carries out supplementary functional tests also, which are not required by regulations, on finished products and on the various components, both in the development stage and in daily production, carried out through the taking of samples. Overall, the aforementioned activity results in the testing of approximately 2,000 helmets every year.
CNC MACHINING
After the R & D center makes 3D data, it will be handed over to CNC to make molds.The term CNC stands for 'computer numerical control', and the CNC machining definition is that it is a subtractive manufacturing process that typically employs computerized controls and machine tools to remove layers of material from a stock piece—known as the blank or workpiece—and produces a custom-designed part. The spare parts produced by CNC automation have no obvious defects and are relatively fine.
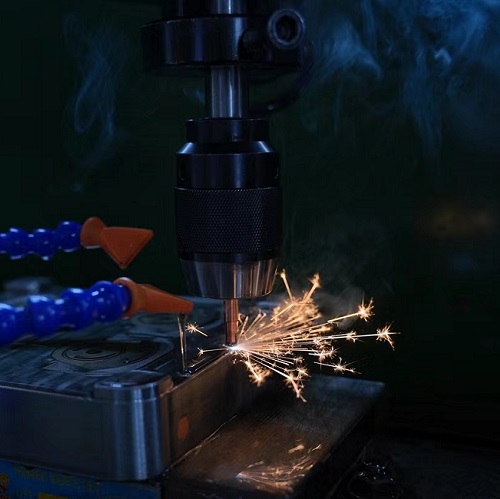
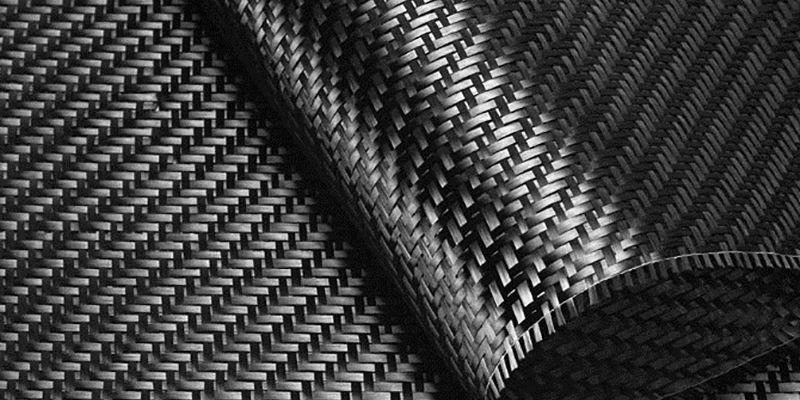
MATERIAL
Aegis specializes in composite material helmets. Know- how and research in the production of Carbon/ Kevlar / Fiberglass is fundamental to Aegis.
MULTICOMPOSITE EVOLUTION
The use of the best materials for us is not enough. The continuous researches and experiments have brought Aegis a position to produce helmet shells that are extremely strong but light.
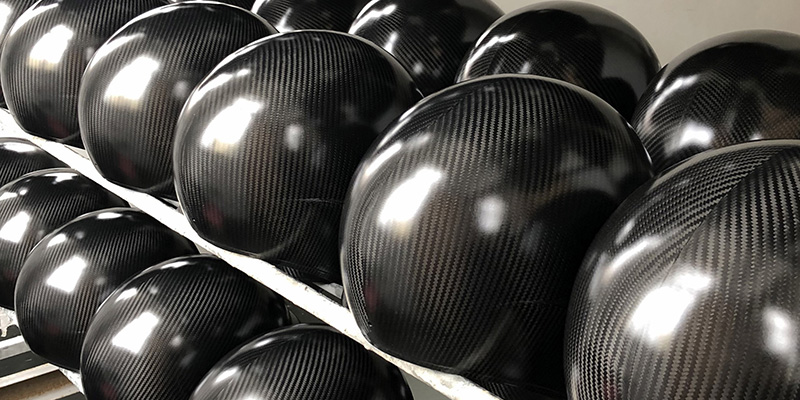
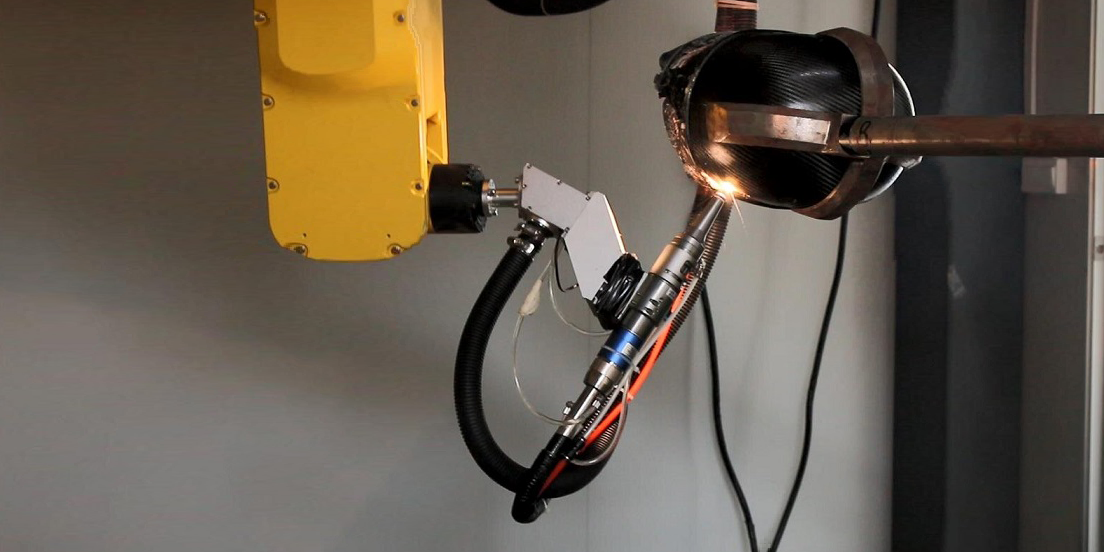
LASER CUTTING
Here the helmet is given its final shape. All the protrusions that area created in manufacture are cut off. The openings for the visor and ventilation are burnt into the helmet shell with a laser. Finally the helmet is checked to ensure that it has the correct material thickness and weight.
PAINTING
Even though many production steps have been automated today, it is not possible to dispense with hand work in some areas. Aegis combines hand work and automation in production to guarantee a very high quality standard in all the details.
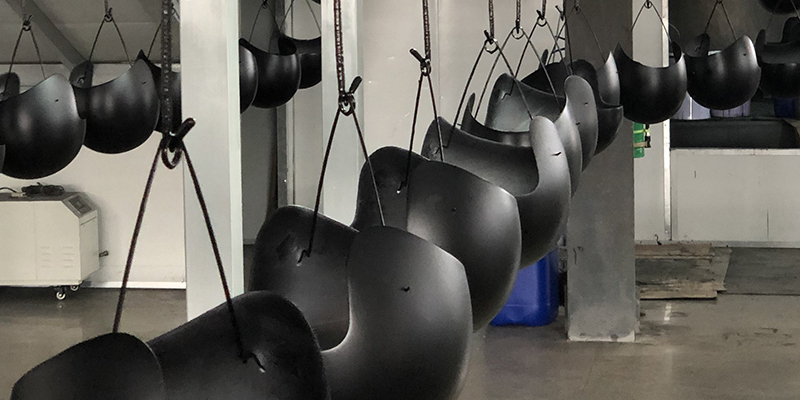
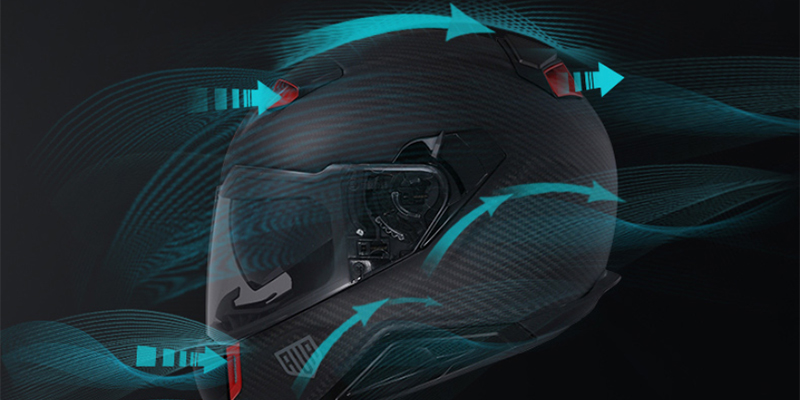
VENTILATION SYSTEM
Ventilation is more effective if air has a way out. Aegis helmets are equipped with air ventilation and extractors which together with the air channeling system inside the polystyrene protection ensure that the user maintains optimal temperature inside the helmet. The air enters the front the flows into the inner EPS shell and comes out at rear extractors, thus obtaining optimal comfort even for long journeys.